Sustainability
Supply Chain Management
The Group is determined to extend our sustainability efforts to the broader supply chain. We exert our influence as a leading professional sports brand with an extensive distribution network and utilize our purchasing power to promote suppliers’ sustainable business practices. By integrating ESG-related criteria into the Group’s assessment of potential and existing suppliers, we ensure supply chain partners fulfil our sustainability requirements. Please refer to our Supplier Corporate Social Responsibility Management Manual below for further details.
Supplier Corporate Social Responsibility Management Manual
To address stakeholders’ concerns about product quality and safety, the Group implements various product quality control measures, including regular monitoring and assessing suppliers’ performance. The different initiatives ensure consistent, high-quality products are manufactured and minimize the risk of large-scale recalls.
Supplier Assessment and Management
As a leading sports brand, we are dedicated to expanding our sustainability efforts throughout our supply chain. Leveraging our market leadership and purchasing power, we encourage suppliers to embrace sustainable practices. To ensure that suppliers align with our sustainability requirements, we have integrated ESG criteria into our supplier assessments for both prospective and existing suppliers.
In May 2023, the Group updated its Supplier Corporate Social Responsibility Management Manual in line with the China CSR Due Diligence Guidance and the relevant requirements of the industry to better achieve the sustainability with its critical business partners. The Manual is now available in the Xtep website.
Our Supplier Portfolio
Our production relies heavily on the materials provided by our suppliers, from whom we source most of our product components. As of 2023, 69% of our footwear and 89% of our apparel manufacturing were outsourced. The Group engages with 573 suppliers globally, with 569 in Mainland China and 4 overseas.
We classify our suppliers into different tiers to better understand our supply base. To strengthen risk management across our supply chain, we have refined definitions of supplier classification this year by broadening the Tier 2 scope and including raw material providers as Tier 3. As of year-end, we have 150 Tier 1 suppliers and 423 Tier 2 suppliers. Going forward, improving engagement with Tier 3 suppliers remains a focus as we seek to optimise sustainable operations.
Definition:

Supplier ESG Management
Our supply chain network involves various environmental and social risks, and we carry out comprehensive, fair and transparent procurement procedures to minimise such risks. The Supplier Management Centre and dedicated teams from different brands work closely with suppliers to ensure high performance. We encourage all suppliers, business partners, and associates to uphold standards on environmental, social, and ethical business practices that align with the Group’s requirements. All these requirements are demonstrated in our Supplier Code of Conduct and Supplier Management Manual, and we expect our partners to comply with them throughout our collaboration.
New supplier admission process
We strictly screen all potential suppliers through an initial qualification and compliance review conducted by the Supplier Management Centre (SMC), and suppliers who pass this initial screening will be subject to on-site audits carried out by personnel qualified as internal auditors from our supply chain development, quality control, and operations departments. This on-site inspection is applicable to suppliers including those providing raw materials for footwear and apparel, auxiliary and packaging materials, finished goods production, semi-finished goods production. Relevant requirements have been communicated to suppliers through our Supplier Code of Conduct.
In 2023, we elevated our social responsibility audit requirements at the supplier admission phase to screen out suppliers that fail to meet our social responsibility requirements. During the year, we introduced 32 new formal and temporary suppliers into our network, and declined the admission of two suppliers due to safety performance concerns. The suppliers were requested to properly address and rectify the safety risks identified for further supplier admission processes.
For overseas suppliers, we appoint third-party suppliers to conduct supplier audits covering aspects such as forced labour, health and safety, child labour, wages and benefits, working hours, discrimination, environmental protection and counterterrorism.
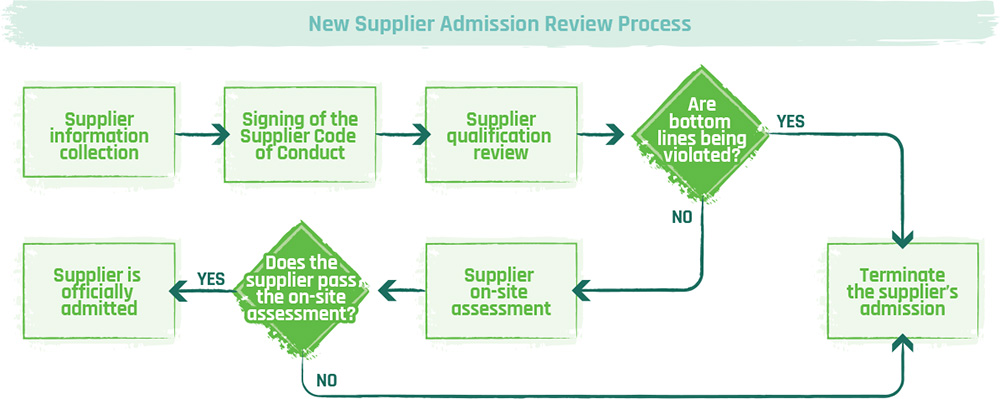
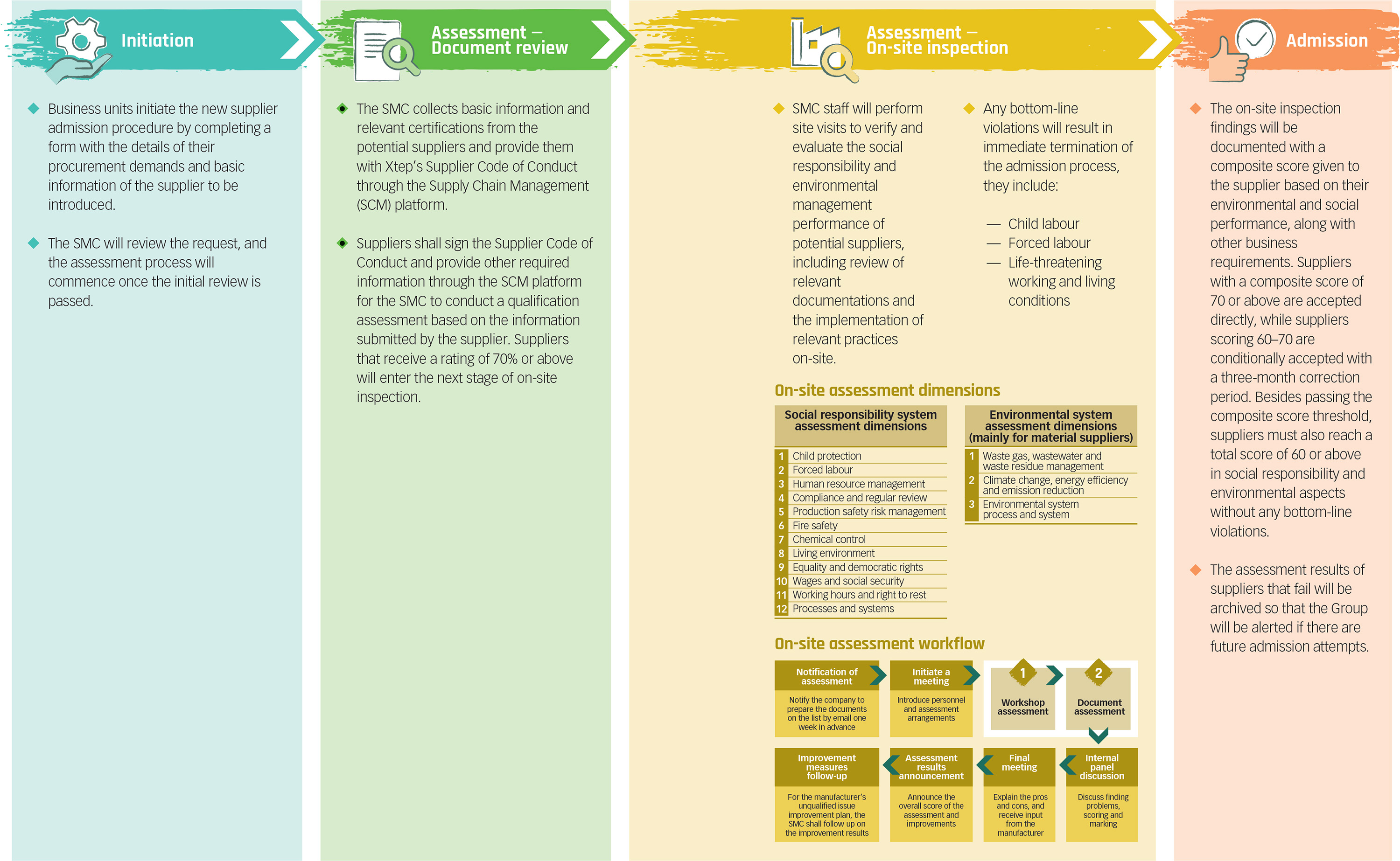
Ongoing supplier evaluation
Existing suppliers are also assessed through document review, on-site inspections, and employee interviews. Between October and December 2023, the Xtep core brand conducted annual assessments on all major garment and finished products suppliers, covering more than 90% of our core Tier 1 suppliers. The audit for Tier 2 on material suppliers will begin in 2024.
47 Tier 1 suppliers of the Xtep core brand were audited, including those producing garments, shoes, and embroidered items. 34% of the assessed suppliers exceeded our requirements, while 42% met the criteria and 23% performed below our expectation. The increase in suppliers not meeting our expectation was mainly due to the upgrade in our assessment standards, and among these suppliers three of them were suspended after further assessments. The remaining suppliers that did not meet our expectations were requested to implement rectifications before the end of June 2024.
For new brands, we primarily conduct annual third-party audits on footwear products, focusing on human rights and counterterrorism. We produce an assessment report annually. Any non-compliance identified will be communicated with the suppliers with rectifications expected within a specified timeframe. A second audit will be conducted to ensure the effectiveness of the rectification measures, and suppliers who cannot meet the Group’s business needs and standards could be terminated. In 2023, all suppliers of the new brands passed the assessment.
The criteria for rating and applying the results of supplier social responsibility assessments are summarised as follows:
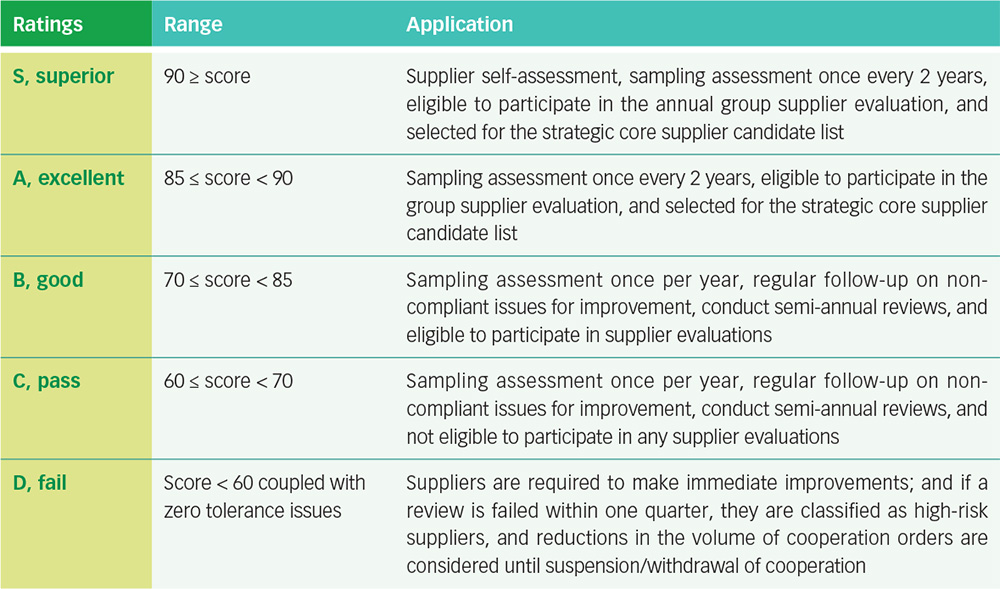
Enhancing Supplier and Build up ESG Capability
To support suppliers in meeting the Group’s expectations regarding environmental and social performances, we continuously engage with our suppliers to understand their limitations and equip them with the skills and knowledge necessary for better ESG performance. These engagements also enable identifying and minimising potential environmental and social risks along the supply chain.
Suppliers’ communication and training
During the year, we conducted ESG training for representatives from our core brand’s footwear and apparel suppliers. A total of 45 supplier representatives attended these sessions, where we emphasised our expectations on social and environmental practices and prmoted suppliers’ awareness towards supply chain sustainability.
Additionally, we engaged third-party experts to organise regular training on ESG matters for our overseas suppliers. Furthermore, we provided unified training on anti-corruption policies for new employees of our new brands. The outcomes of all these training sessions were deemed satisfactory.
Product and Material Quality Assurance
Quality assurance is crucial to our production processes. Our products are subject to stringent quality control tests, which help ensure that only items that meet the Group’s quality requirements are sold to our customers. Our quality control teams are responsible for the quality control processes, which include sample testing and inspection to enhance supplier quality control.
Product Quality Control Process and Procedures
We have a ISO9001-certified quality management system to ensure the quality of our own productions through standardised production process. In the R&D phase, our standards team conducts thorough testing and verification of products and materials to develop standards suitable for mass production. This year, we also implemented new management specifications for clothing carton stacking and down storage operations. In 2023, the Standards Team had created and revised 22 pieces of clothing quality standards (including 14 enterprise standard filings and 8 internal control standards) and participated in drafting 6 national clothing standards and revising 39 national standards, all aimed at improving the quality management system.
In September 2023, Xtep organised a discussion session to improve the physicochemical testing of mesh materials used in footwear, with participation from mesh suppliers, technicians, subcontractors, and representatives from finished product factories. The discussion focused on the specific requirements for the use of new materials. Xtep emphasised the need for a comprehensive assessment and mitigation of potential risks during the early design phase of development, as well as the necessity for refinement in the selection of raw materials and process operations, with strict adherence to established protocols.
In this year, Xtep has received product quality recognitions from various organisations:
- The Director of Xtep’s Quality Management Centre was awarded the “Advanced Individual in Standardisation Work,” enhancing Xtep’s discourse power in textile and apparel industry standards and improving the brand’s reputation.
- Xtep’s Apparel Testing Centre participated in the “Fibre Inspection Cup” testing skills competition organised by the Fujian Fibre Inspection Bureau. Five testing engineers participated and won the first prize in the group knowledge competition.
At the production stage, the quality management teams monitor the quality and safety of raw materials and finished products. They also perform regular quality control activities on the production process and conduct stringent product quality inspections to ensure the finished products from our suppliers pass physical and chemical standards before being delivered to customers. In addition, Xtep conducts monthly sample testing for its Tier 1 and Tier 2 suppliers. Raw materials, adhesives, and finished products are sent to nationally certified third-party laboratories every quarter, ensuring the final products align with national standards and product quality and safety regulations.
To improve product quality, the Group established a special quality control circle for items like down jackets and shoes, allowing steady quality enhancement for specific product categories. The team also conducts competitive product analysis to optimise product standards and testing methodology while promoting product quality and comfort.
Case study
In 2023, we organised an ISO9001 Quality System Manager Training Camp, where all 51 participants passed the assessment and were awarded the “Quality Management Systems — Internal QMS Auditor Certificate”.
The group also enforces stringent quality control procedures for outsourced productions, and monthly quality review meetings are conducted to ensure proper quality management. We consistently enhance our employees’ capabilities in product quality management, and support our staff to participate in training such as the anti-mould measures training by Micropak and testing procedures training by SATRA. In 2023, to improve product quality and manufacturing processes, K·SWISS and Palladium introduced automated screen-printing machines, laser machines, high-quality computerised automatic threading machines, computerised sewing machines, digital printing, and other equipment and technologies, while also implementing a fully enclosed eco-friendly assembly line.
To stay informed on the feedback of our customers, our sales department discuss weekly with our supply chain management departments and our quality management team will visit physical stores to understand market trends and customer needs.
Enhancing Product Quality Control with Suppliers and Customers
We proactively help our suppliers build quality control and management capacity to promote the Group’s overall product quality. We have provided training on testing knowledge and professional skills enhancement for external cooperative suppliers and laboratory personnel, followed by assessments and certifications. This helped improve the quality management systems of our suppliers and by the end of 2023, 33 supplier laboratories had been certified, covering garment, printing, materials, and accessories suppliers.
We delivered FQC/IQC certification training to Tier 1 and Tier 2 suppliers to foster self-regulation in supply chain quality, improve product standards, and support beneficial supply chain growth. Additionally, we organised 17 training sessions on apparel quality standards, engaging around 280 internal and external supplier representatives
Customer Relationship Management and Satisfaction
At Xtep, we adopt a consumer-first approach, ensuring open communication with our customers to meet their needs. We systematically handle complaints by setting resolution timelines, monitoring progress, and working towards mutually agreeable solutions to enhance customer satisfaction.
We have established protocols for product recalls and quality issues. In the event of a significant recall, our Quality Management Centre conducts thorough investigations, reports findings to senior management, and corrective actions are taken to prevent future occurrences. In 2023, we had no significant recalls due to health or safety concerns. We assure customers of repair, replacement, or return of local products sales, and the Xtep core brand has implemented a robust product return program, with our comprehensive Return and Exchange Policy allows for unconditional acceptance of worn products.
Our dedicated “400 Hotline” is the first point of contact for customer complaints. Complaints are recorded, verified, and typically responded to within 2 business days, with specific resources reserved to address individual cases that are complex in nature. The number of complaints received through the “400 Hotline” in 2023 was 4,7556. We also conduct monthly callbacks to gauge customer satisfaction and invite feedback from all “400 Hotline” users. In 2023, we achieved a 92.88% satisfaction rate, which is higher than the original target of 90%.
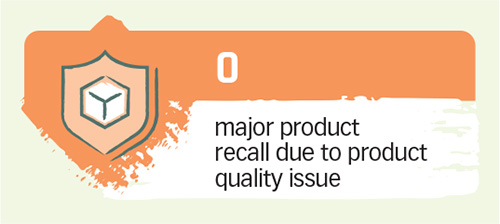
We enhanced the “400 Hotline” this year with an improved voice navigation system for more efficient paring between callers and live operators. As a result, our customer service reception capacity has increased by over 300%, and our hotline connection rate has improved by 35%.
6 There has been a notable increase in the number of customer complaints, primarily driven by the rise in product sales during the year. However, the ratio of complaints to total inquiries has decreased compared to 2022.